
Дизайнеры — о производстве: конспект паблик-тока во Всероссийском музее декоративного искусства
Какие стадии проходит дизайнер от первой идеи до готового продукта? Как снизить себестоимость изделия, не потеряв его привлекательность? И почему в России сложно найти производителя? В конце зимы в Центре моды и дизайна Всероссийского музея декоративного искусства в рамках проекта «Придумано и сделано в России» прошел паблик-ток «Дизайн и производство». Молодые дизайнеры, художница по текстилю и керамист рассказали о том, как они искали производство и с каким трудностями сталкивались. Мы записали эти истории.
Конкурс «Придумано и сделано в России» будет проходить в формате биеннале. В рамках подготовки второго конкурса, который пройдет в 2020 году, организаторы вместе с дизайнерами исследуют актуальные вопросы индустрии, один из которых — связь дизайна и производства.
Сергей Гравчиков, дизайнер, сооснователь марки Unika Moblar
Часто цикл с момента, как ты придумал вещь до того, как компания запускает ее на рынок, равен очень короткому сроку. Нужно успеть сделать прототипирование, убрать все ошибки разработки и довести изделие до серийности, чтобы оно было экономически целесообразно. Бывает, делаешь вещь в 3D, смотришь каждую деталь, проверяешь с разных ракурсов все сочленения и в трехмерном объеме кажется, что все хорошо. Потом на этапе прототипирования, когда делают первый предмет, понимаешь, что за счет ракурса ты сам себя обманывал. Мы смотрим сверху, снизу, сбоку — отовсюду, а человек, который, пользуется стулом, смотрит только с двух точек: вот он стоит, вот он сидит, и все.
Еще в прототипе мы считаем тайминг: сколько времени занимает сборка стула, шлифовка и так далее — без четкого расчета экономики в не сможешь сказать, сколько будет стоить твой продукт на выходе. Наш следующий шаг — сделать полукресло полностью разборным и упаковать в плоские коробки, чтобы сильно сократить стоимость при доставке. Дальше идет проверка цветом. Мы пробовали разные варианты покраски, и в итоге нашли неочевидный вариант: пропитываем первый слой фанеры морилкой на максимальную глубину, до 1-1,5 миллиметра, потом кроем грунтом, делаем еще цветной грунт и потом финиш. Получается, даже если и происходит скол, под ним видно черное дерево.
Изначально у нас была попытка отладить производство на аутсорсе. Она какое-то время держалась, но шансы эффективно контролировать качество дистанционно очень малы. В итоге мы объединились и стали заново выстраивать цикл производства, пытаясь автоматизировать его и сократить. Сейчас у нас на производстве работают 15 человек. Не могу сказать, что все они энтузиасты, но 10 из них — точно.
Ольга Никич, художник по текстилю
Я рисую от руки, а потом сканирую и обрабатываю рисунок в векторной программе. Если бы я отдавала изображения кому-то на обработку, пришлось бы быть гораздо аккуратнее. А так я сама дорабатываю все на компьютере и знаю, чего в итоге хочу добиться, поэтому изначально довольно легко обхожусь со своими эскизами. После отрисовки я могу легко менять цвета, усложнять или добавлять слои. Это удобно, потому что макет можно сразу напечатать в технике шелкографии. Платок «Трактористка» был сделан именно так.
У меня нет своего производства, поэтому я сотрудничаю с компаниями на аутсорсе. Кроме шелкографии я использую цифровую печать — это довольно высокотехнологичная и дорогая вещь, поэтому у нас в стране таких машин немного. Я знаю три места в Москве, где можно печатать цифровым методом. Их сложно контролировать, и это большая беда наших производителей. Нет стабильности, приходится за ними ходить, стоять за спиной и требовать, чтобы все было сделано на должном уровне. Печать на шелке — сложный многосоставной процесс: ткань сначала должна быть пропитана закрепляющий составом, чтобы краска не растекалась, а после печати состав нужно смыть, а ткань высушить. Те есть в процессе участвуют целых три машина. Затем полотно снимается, режется и подшивается. Обычно при создании образцов ты сначала выбираешь ткань, которую тебе прислали с производства, потом заказываешь пробную печать, смотришь, как вел себя цвет и на какой ткани он лучше смотрится, и только потом выходишь на тираж.
Андрей Будько, дизайнер
Проект Carpet like a Russian — это моя профессиональная рефлексия на тему «ковра на стене». Это мой второй заход в дизайн. Восемь лет назад я открыл свое производство, а три года назад закрыл и с этого момента стал думать о проекте с коврами. Сейчас я работаю с производствами на аутсорсе. Сначала я предполагал, что просто придумаю веселый ковер и буду его ткать. Но исследование этой темы показало, что два самых четких воспоминаний о коврах — это пыль и моль. Я не хотел делать очередной пылесборник и стал искать новое решение. Войлок — нетканый материал и пыль в него не набирается. Вышивка тоже пришла в процессе. Я пробовал разные варианты, делал аппликации, думал про печать, но только вышивка оказалось под стать прочности и износостойкости войлока.
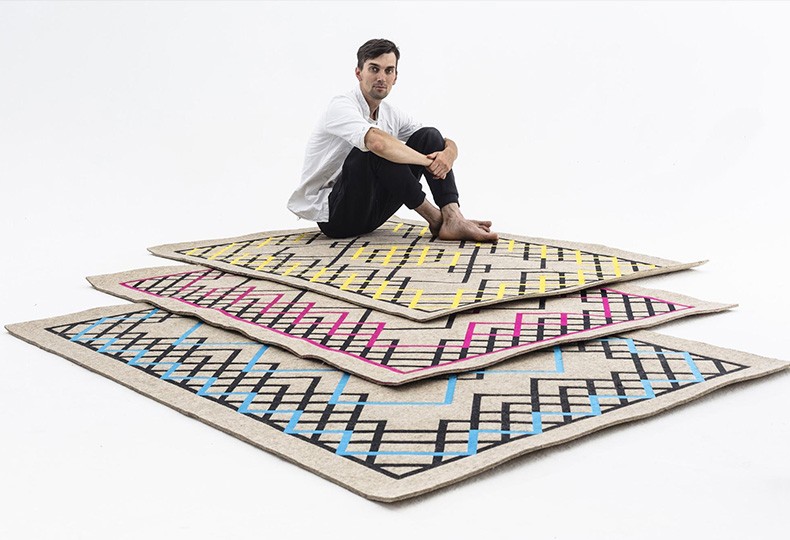
Сложность в том, что ковер, который я придумал, находится за гранью технических возможностей производств. В России сейчас вышивальные машины в основном используются для изготовления сувениров, шевронов, надписей на футболках и бейсболках. Задача такого станка — копировать.
В моем лонг-листе было 117 фабрик, из Москвы, Санкт-Петербурга, Иваново, Ярославля, Тверской области. На 22 из них я съездил, чтобы поговорить, и с восемью начинал работать. Не считая пробных вариантов, полноразмерных, близких к окончательному дизайну, было сделано 12 образцов. Сейчас, спустя 2,5 года у меня до сих пор стоит проблема производства. Качество меня устраивает, но не получается обеспечить его стабильность: основная сложность заключается в стыковке вышиваемых частей в один большой неразрывный узор. Безусловно цена каждой итерации достаточно большая, и параллельно я работаю над дизайном другого ковра без такой четкой стыковки рисунка, деньги от продажи которого смогу для реализации первой коллекции.
Полина Шутова, дизайнер
Мой проект называется «Плетение» — это 3D-печать из керамики. Сама технология очень простая, особенно если ты уже занимался керамикой и представляешь, как из нее лепить. Фактически, это самая простая техника — лепка жгутом. Просто вместо руки здесь — «сопло», через которое из баллона с помощью компрессора подается глина. Головная часть с чипом принимает сигнал от компьютера и идет по заданной траектории. Это совсем несложная конструкция, собранная из брусков, трубок и изоленты.
Можно сказать, что это совместная работа художника и программиста — мы написали свой код. И так, как это был мой первый опыт, я делала все 3D Max: создала такую форму, чтобы читалась оправданность этой горизонтальной текстуры, которая получается при послойной печати. Одной из моих целей было, как раз, добиться сложного вида при изначально простом формообразовании.
Ольга Подольская, дизайнер интерьеров, предметный дизайнер
Светильники FireFlies я разработала для петербургской компании Handle Studio.
Изначально форма светильников была не такая сложная, и плафоны предполагалось делать из толстостенного стекла. Но, к сожалению, производство выдувного стекла у нас не очень развито и светильники казались похожими на уличные фонари. Тогда я решила использовать хрусталь, который благодаря граням и преломлению света давал бы нужный блеск и яркость. За производством я обратилась на завод «Гусь-Хрустальный».
На заводе по эскизам сделали два варианта граней: продольные и ромбовидные. А когда пришли первые экземпляры, мы поняли, что во втором варианте нужно добавлять еще один ряд, чтобы не было видно лампочку. Во время создания образцов мы работали дистанционно, но потом я ездила туда, чтобы непосредственно познакомиться с производством.
У меня есть опыт создания светильников и керамической плитки для итальянских марок. В России тоже можно изготовить предмет, но поражает его стоимость: любое изделие, которое я делала и рассчитывала в России, в Италии всегда оказывалось дешевле. Единственное исключение, пожалуй, — это кухни: в России и они получаются дешевле итальянских.
Дарья Яроменок, керамист
Комплект «Кольца» — мой дипломный проект, часть которого я реализовала на Императорском фарфоровом заводе. Задачей было сделать форму максимально лаконичной и подходящей для серийного производства.
Первый этап работы — проектирование. Именно на этом этапе выбирается тип массы, с которой предстоит работать и закладывается форма. Происходит это так: дизайнер делает чертеж, приходит на завод и корректирует его с технологами предприятия. Фарфор – масса невероятно капризная. Она становится очень пластичной при обжиге, деформируется, дает сильную усадку, которая доходит до 20% в зависимости от массы. Учитывая все это, изначальная форма претерпевает изменения.
Следующий этап – формовка. Сначала делаются модели. В гипсовую форму заливается жидкая глина, гипс впитывает влагу, обезвоженная глина начинает оседать на стенках, и образуется черепок изделия. Как только черепок набирает нужную толщину, излишки сливаются, и спустя некоторое количество часов достают само изделие или его детали, которые потом склеиваются. Моя ваза была разбита на две детали: внешняя чаша и внутренний стакан, отверстие внутри прорезали отдельно. Потом идут сушка и обжиг.
Моя форма достаточно простая для изготовления — как раз для серийного производства. Я продолжаю сотрудничать с ИФЗ и собираюсь воплотить на их производстве новый проект.
Анна Кислицина, основатель марки «Кофесумка»
«Кофесумка» это не только сумки, но и рюкзаки, косметички из кофейных мешков. Проекту три года. Идея появилась несколько раньше, но довольно много времени ушло на то, чтобы запуститься. Было очень сложно: я никогда не занималась тканями, не была знакома с материаловедением, а тут ко мне попал джут — капризная ткань, плотная, ворсистая, сыпучая. Было не понятно, как с ней работать.
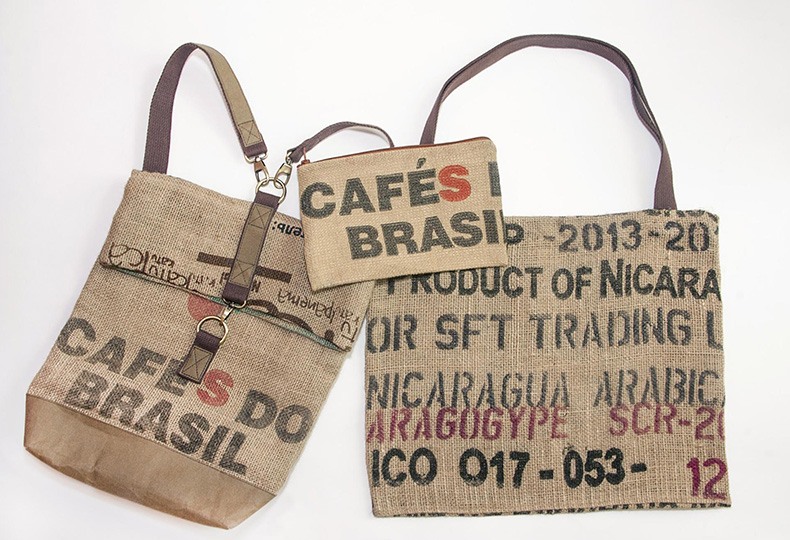
У меня в голове был стереотип, что производство — это некий цех, студия с оборудованием, где сидят люди и делают все «от и до». Много времени ушло, чтобы понять: мир изменился, и сейчас производство может быть полным, а может — рассредоточенным. Сейчас у меня есть студия, где я делаю крой и планирую модели, отдельно существует швейное производство, отдельно — курьерская служба. Для меня это самая устойчивая система, и она работает.
Мой самый успешный продукт — это «Легкая кофесумка», сумка-шоппер без подкладки и застежки. Я создавала ее как чисто летний вариант, но она стала супер популярной. Такая сумка стоит 1000 рублей, в свернутом состоянии она размером с кулачок — ее можно положить даже в клатч, а в развернутом — она объемная и выдерживает значительный вес.
Петр Сафиуллин, архитектор, основатель студии дизайнерской мебели Yaratam Design
Я занимался архитектурой и интерьерами, и во все свои проекты проектировал предметы сам. В конце концов у меня появилась мысль производить некоторые вещи серийно. Долгие попытки наладить сотрудничество с мастерскими оканчивались одинаково плохо, и тогда я решил сделать свое производство — сейчас ему два года. Вместе с товарищем, который заинтересовался идеей, мы нашли цех со станками, взяли мастеров, которые работают с деревом, и начали производить мебель.
Первые полтора года мы работали «в ноль»: фактически я был единственным заказчиком и кормил производство, делая предметы для своих интерьерных проектов. Параллельно мы пытались выпускать серийные вещи. Обороты начали расти, людей не хватало, помещение было маленькое, а станки — ужасные, и мы ничего не успевали. Я понял, что нужно что-то менять, и летом 2018 года мы перезапустили производство: сняли другое помещение и купили хорошие станки. Инвесторов мы не привлекали — я вкладывал в производство те деньги, которые сам заработал. Сейчас мы продаем нашу мебель через инстаграм и интернет-магазины и ведем переговоры с несколькими московскими шоу-румами.